text.skipToContent
text.skipToNavigation
The brand-new Preventa XPS Universal range of safety modules is designed to simplify the user’s life (both in terms of choice and use). It provides differentiated diagnostics for cable architectures (40 different status messages) without a fieldbus interface. In addition, the range is able to provide status information on the verification test intervals to be performed and the number of remaining end-of-life cycles. To make the choice even easier, the safety functions can be selected directly on the housing, which significantly reduces the number of references and therefore the number of required spare parts.
Preventa XPS Universal combines the simplicity of wired safety modules with a variety of messages that in the past required complex and expensive fieldbus technology. With a simple point-to-point connection using an ordinary cable between the intelligent output and the digital input of a PLC, the Preventa XPS Universal safety modules can send more than 40 different messages.
In addition, thanks to an intelligent auxiliary output, the safety modules provide information about upcoming test cycles and the number of remaining end-of-life cycles.
How does it work? The Preventa XPS Universal safety modules send modulated signals to the machine controller. The machine builder provides two function blocks in the machine driver to decipher these signals. In order to simplify commissioning, Schneider supplies a library of function blocks for all the programming systems of the Schneider Electric PLCs and the programming systems of the most common PLCs available on the market.
This makes the Preventa XPS Universal safety modules the best choice for a wide range of simple to moderately complex machines: easy to use because integration is always based on a wired connection and no field bus is required.
The modules are an answer to the demand for differentiated diagnostic information and the approaches towards preventive maintenance. Each reference from the range of safety modules can be adapted to several safety functions. The functions can be set with a finger or a screwdriver by turning the rotary switches on the front. Its multifunctionality makes it possible to reduce the number of references, while offering a wide variety of safety functions, and at the same time to limit the logistics and documentation of a machine.
Certified plug-and-play solutions are already available. The certified safety solutions from Schneider Electric are examples of applications with documented architecture. This allows reliably defined safety functions to be provided and the development of protected machines to be accelerated.
Some technical features of the Preventa XPS Universal range of safety modules:
Read further
A completely new and easy to use range of safety relays
The brand-new Preventa XPS Universal range of safety modules is designed to simplify the user’s life (both in terms of choice and use). It provides differentiated diagnostics for cable architectures (40 different status messages) without a fieldbus interface. In addition, the range is able to provide status information on the verification test intervals to be performed and the number of remaining end-of-life cycles. To make the choice even easier, the safety functions can be selected directly on the housing, which significantly reduces the number of references and therefore the number of required spare parts.
Preventa XPS Universal combines the simplicity of wired safety modules with a variety of messages that in the past required complex and expensive fieldbus technology. With a simple point-to-point connection using an ordinary cable between the intelligent output and the digital input of a PLC, the Preventa XPS Universal safety modules can send more than 40 different messages.
In addition, thanks to an intelligent auxiliary output, the safety modules provide information about upcoming test cycles and the number of remaining end-of-life cycles.
How does it work? The Preventa XPS Universal safety modules send modulated signals to the machine controller. The machine builder provides two function blocks in the machine driver to decipher these signals. In order to simplify commissioning, Schneider supplies a library of function blocks for all the programming systems of the Schneider Electric PLCs and the programming systems of the most common PLCs available on the market.
The Preventa XPS Universal safety modules: the best choice for simple to moderately complex machines
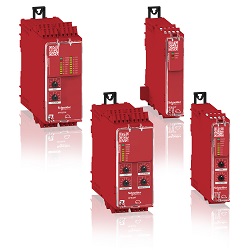
The modules are an answer to the demand for differentiated diagnostic information and the approaches towards preventive maintenance. Each reference from the range of safety modules can be adapted to several safety functions. The functions can be set with a finger or a screwdriver by turning the rotary switches on the front. Its multifunctionality makes it possible to reduce the number of references, while offering a wide variety of safety functions, and at the same time to limit the logistics and documentation of a machine.
Certified plug-and-play solutions are already available. The certified safety solutions from Schneider Electric are examples of applications with documented architecture. This allows reliably defined safety functions to be provided and the development of protected machines to be accelerated.
Some technical features of the Preventa XPS Universal range of safety modules:
- protection against unwanted alterations: front with a transparent flap that can be sealed to cover the selector switches.
- extension module: no external cabling required (except XPSU-AB and XPSU-EP).
- extensive choice of delay times: choice from 0.1 to 900 seconds for machines with weak or high inertia.
- compact modules, flexible mounting: width 22.5 and 45 mm, DIN rail or direct wall mounting (housing IP40, clamps IP20)
- 2 power supply options for all references: power supply 24 VAC / DC + extended power supply 48 ... 240 VAC / DC
- options with removable spring clamps for all references
You might also be interested in this:
Schneider Electric PacDrive3
Read further
PacDrive 3 is based upon proven logic motion technology, which unifies PLC, motion, and robotics control functionality on a single hardware platform. With its centralised system architecture, PacDrive is the ideal solution for controlling a broad range of servo-driven production and packaging machines, as well as material handling equipment and robotics, using fully integrated, IEC 61131-3-compliant program structures. More than 80.000 machines worldwide are controlled by PacDrive to this day.
Schneider Electric XIOT
Read further
The Internet of Things IoT is the extension of the Internet to connected devices. Telemecanique Sensors offers a wireless solution to collect data from remote equipment and use this data, via the Internet, on a PC or mobile device. The XIOT Cloud connected switch from Telemecanique Sensors is based on low power wide area network technology, operated by Sigfox. The Sigfox network covers 32 countries and is already very extensive in Europe. It is also being rapidly deployed in the US and Asia-Pacific. It uses antennas with a range of around 50 km. The map on the Sigfox website shows exactly which areas are covered by the Network.
Schneider Electric TeSys Island
Schneider Electric TeSys Island
TeSys™ island is a digital load management solution that makes machines smarter and more reliable. It is a fully digitized, object-oriented load management system and an Industry 4.0 compliant data provider. It reduces machines’ time to market enabling OEMs to move forward in their Industry 4.0 journey. TeSys island gives users easy & remote access to predictive & preventive application data, leading to early diagnostics & maintenance.
Schneider Electric has expanded its range of Altivar 320 frequency converters with a version with increased IP protection like dust and water, especially developed for placement in the installation close to the motor.